Cutting-Edge advancements in 3D Printing for Aircraft Components are the cornerstone that propels us forward into a future defined by groundbreaking technologies. One such transformative force making waves in the sector is the integration of 3D printing in the manufacturing of aircraft components. As industry specialists, we recognize the pivotal role that this technological marvel plays in shaping the future of aerospace and defense.
Thank you for reading this post. Don't forget to subscribe!
Unveiling the Prowess of 3D Printing in Aerospace
A Paradigm Shift in Manufacturing
Aerospace and defense manufacturers are undergoing a profound transformation as they embrace the limitless possibilities offered by 3D printing. This revolutionary technique enables the production of intricate and complex components with unparalleled precision, previously unattainable through traditional manufacturing methods.
Enhanced Design Flexibility
With 3D printing, the design limitations that once constrained aerospace engineers are now a thing of the past. This technology grants unprecedented freedom in crafting intricate geometries, optimizing structural integrity, and reducing overall weight without compromising performance—a crucial factor in the realm of aviation.
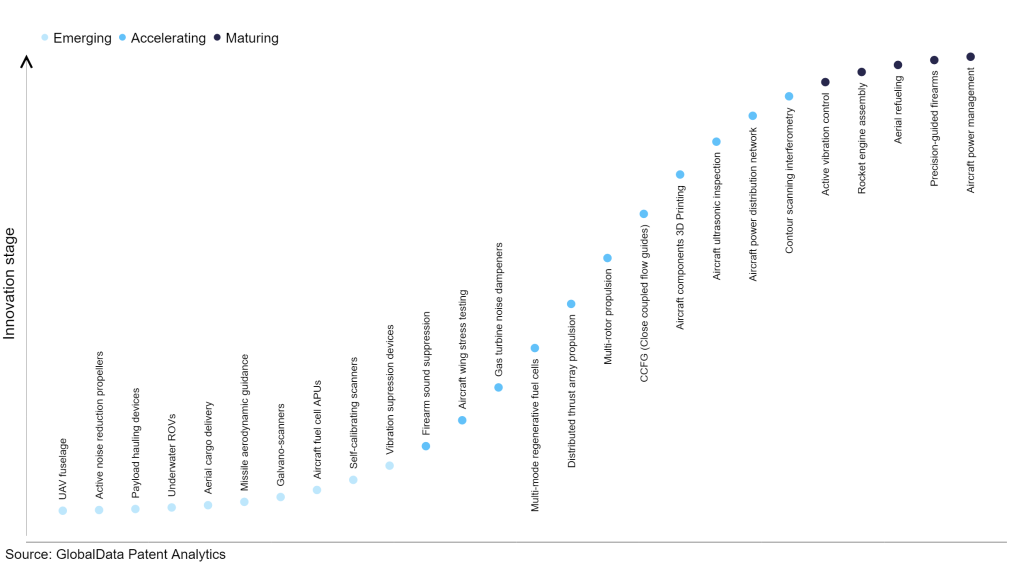
The Intersection of Innovation and Efficiency
Streamlining Production Processes
In an era where efficiency is paramount, 3D printing emerges as a game-changer by streamlining production processes. Traditional methods often involve numerous intricate steps, each susceptible to errors and delays. 3D printing technology minimizes these risks, enabling the rapid production of high-quality components while maintaining rigorous industry standards.
Cost-Effective Solutions
As we delve into the intricacies of aerospace manufacturing, cost considerations loom large. The utilization of 3D printing allows for the optimization of material usage, reducing waste and subsequently lowering production costs. This cost-effectiveness positions 3D-printed components as a compelling alternative in an industry where every ounce and every dollar count.
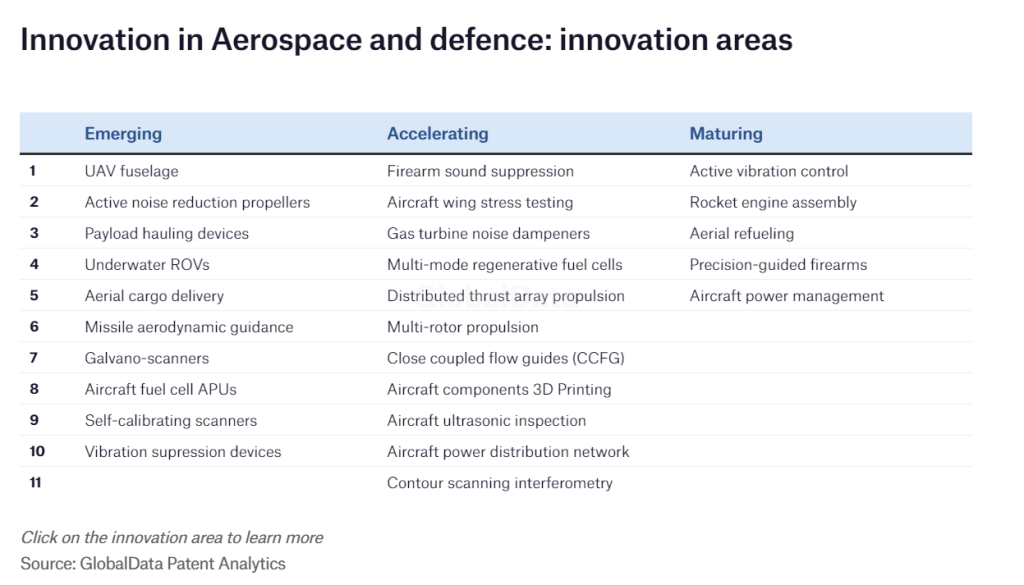
Ensuring Regulatory Compliance and Safety
Stringent Testing and Certification
A paramount concern in aerospace and defense is ensuring the utmost safety and compliance with industry regulations. Addressing these concerns, 3D-printed components undergo rigorous testing and certification processes to meet and exceed industry standards. This commitment to safety underscores the reliability and viability of 3D-printed aircraft components.
Real-World Applications and Success Stories
Aircraft Engine Components
One of the most exciting applications of 3D printing in aerospace is the manufacturing of intricate engine components. The ability to create complex geometries with high precision has led to enhanced engine performance, reduced fuel consumption, and increased overall efficiency, marking a paradigm shift in aircraft propulsion technology.
Lightweight Structural Components
Aerospace engineers are leveraging 3D printing to fabricate lightweight yet robust structural components. This not only contributes to fuel efficiency but also extends the lifespan of aircraft, mitigating the environmental impact of manufacturing and operation.
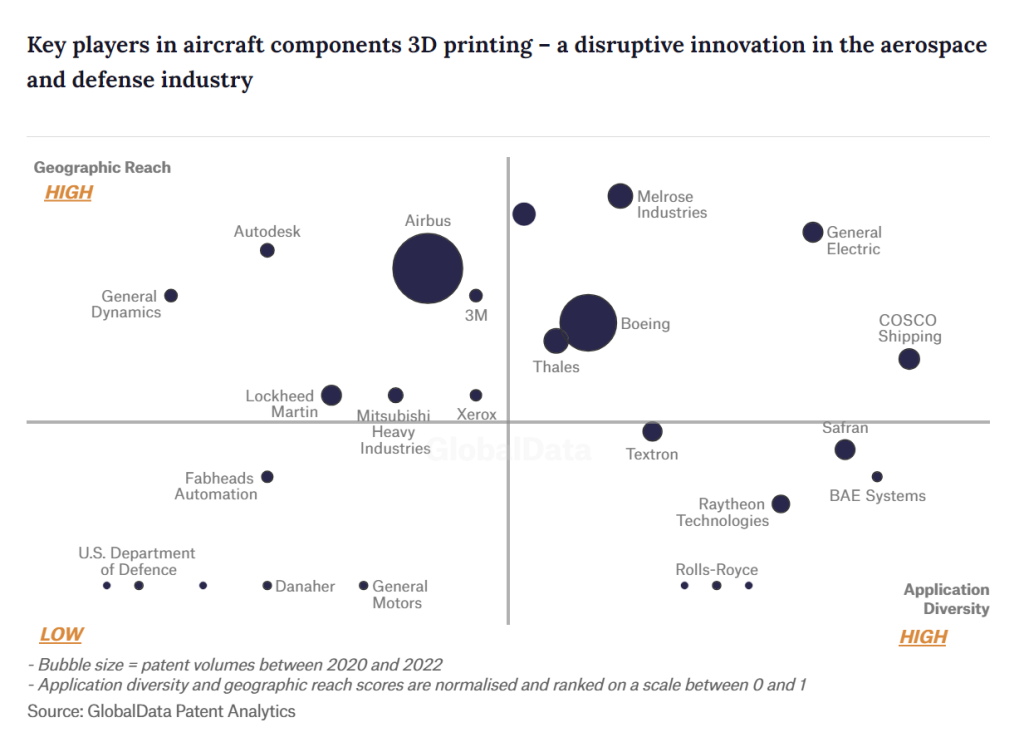
Navigating Challenges and Charting the Future
Material Innovation
As the adoption of 3D printing accelerates, the focus shifts to advancing the range of materials compatible with this technology. Researchers and manufacturers are actively exploring and developing novel materials with enhanced durability, heat resistance, and overall performance to meet the demanding requirements of the aerospace and defense sector.
Scaling Production Capacities
While 3D printing offers unparalleled advantages, scaling production capacities remains a challenge. Industry leaders are investing in research and development to address scalability issues and ensure seamless integration of 3D printing into large-scale aerospace manufacturing.
Conclusion: Paving the Way Forward
In conclusion, the integration of 3D printing in aerospace and defense marks a transformative leap into a future where innovation, efficiency, and safety converge. As dedicated specialists in the field, we recognize the immense potential of this technology to redefine the boundaries of what is achievable in aircraft component manufacturing. The journey ahead involves overcoming challenges, fostering material innovation, and scaling production capacities to ensure a future where 3D-printed aerospace components stand at the forefront of industry excellence.
In this dynamic landscape, our commitment to advancing aerospace technology remains unwavering. Through the lens of 3D printing, we navigate the complexities of the industry, propelling aerospace and defense into a future where innovation knows no bounds.